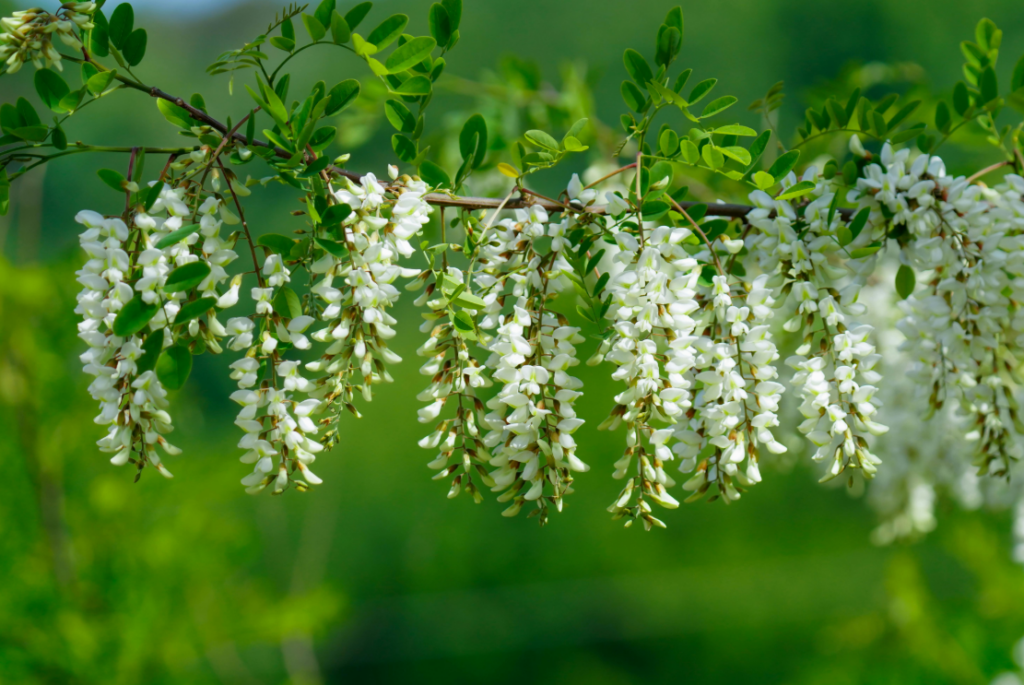
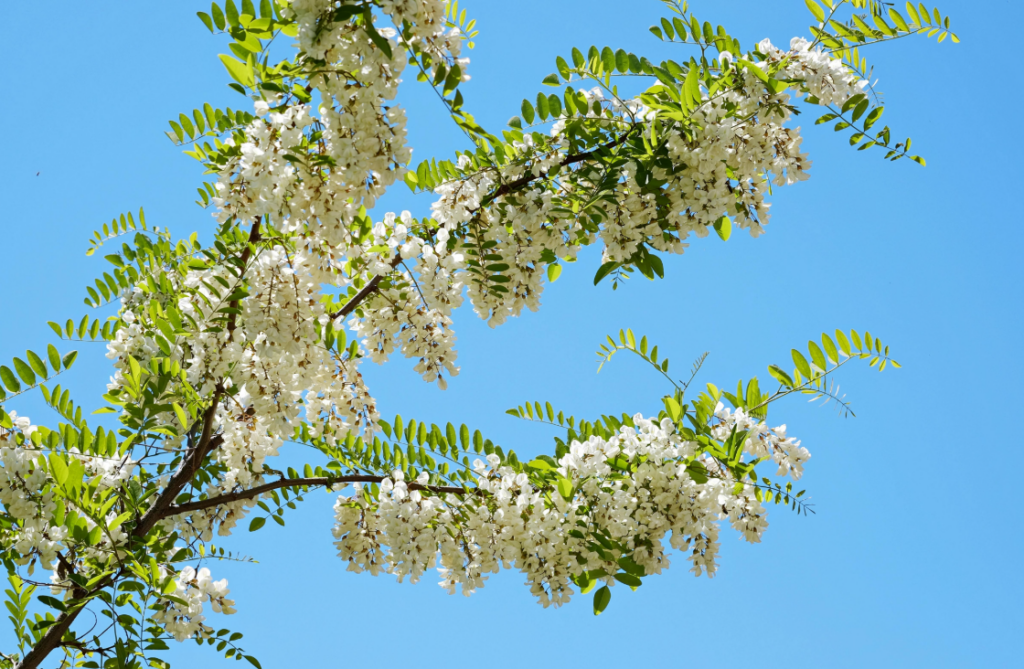
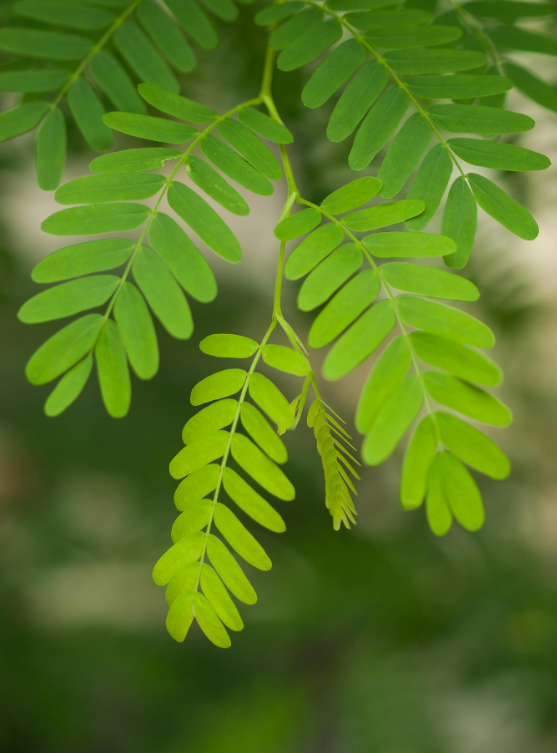
Az akác nagyon szép
Az Akác nagyon illatos fa.
J. ROBIN PÁRIZSI KIRÁLYI FŐKERTÉSZ SOK EGYÉB NÖVÉNYFAJJAL EGYÜTT 1601-BEN HOZTA BE ÉSZAK-AMERIKÁBÓL EURÓPÁBA
More informationJ. ROBIN PÁRIZSI KIRÁLYI FŐKERTÉSZ SOK EGYÉB NÖVÉNYFAJJAL EGYÜTT 1601-BEN HOZTA BE ÉSZAK-AMERIKÁBÓL EURÓPÁBA
More information